Abstract
The thermal effect of the adhesive material of Aluminum Alloy 319 (Al319) on the cutting tool (insert) causes major problems in surface roughness, tool wear, as well as temperature due to the tendency to melt during the cutting process which can lead to the formation of formed edges, inaccuracies of measurement on the workpiece, surface damaged due to oxidation, which can reduce the life of the insert. The objective of this research is to optimize the nozzle cooling system method in the machining performance of Aluminum alloy 319 to achieve good surface roughness, low-temperature reading, and less insert wear by selecting machining parameters appropriate to cutting speed, cutting depth, and feed rate. The variety of orifice nozzle measurements used from nozzles 1.0 mm to 5.0 mm with the use of different machining parameters (cutting and spindle speed and with fixed cutting depth) using on CNC lathe condition. This method is done by the basic reaction surface (RSM), which is one of the alternative methods to minimize the cutting process that can be done at high cutting speed in which the temperature can minimize the formation of wear on the insert. Built-in edges and thermal construction can reduce the roughness of the work surface. The results of this research the smallest orifice nozzle used able to minimize the thermal impact and reduce the temperature that causes the arrangement of lower build edges (BUE). Therefore, better surface roughness, minimum insert use as well as low temperatures can be achieved. This is because the direction of the coolant can be directed at a point that can remove heat from the chips. The use of cutting fluid from the smallest nozzle size and technical conditions in the machining process can also be offered to obtain productivity, high-quality products, lower costs as well as minimize environmental impact (refrigerant waste is generated). This research is very useful to minimize the cost of the machining process budget and also increase productivity in the machining industry and can also decrease the dependency of machine operators on the skills and knowledge available.
Export citation and abstract BibTeX RIS
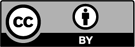
Content from this work may be used under the terms of the Creative Commons Attribution 3.0 licence. Any further distribution of this work must maintain attribution to the author(s) and the title of the work, journal citation and DOI.