Additive manufacturing is an innovative new technology in which layers of materials are added strategically to produce three-dimensional structures. Over the course of recent years, it has undergone remarkable advancements, enabling the realization of intricate designs, shortening production timelines, and causing a transformative shift in manufacturing protocols. This comprehensive article examines the most recent advances and problems in additive manufacturing. The present paper provides a concise overview of the fundamental principles and methodologies of additive manufacturing. Subsequently, it delves into the latest advancements and cutting-edge technologies in this domain, including multimedia printing, bio printing, and metal 3D printing. Finally, this study concludes with future prospects and directions of this technology.
Focus Issue on Additive Manufacturing Processes
Guest Editors
- Liew Pay Jun, Universiti Teknikal Malaysia Melaka, Malaysia
- Nur Izan Syahriah Binti Hussein, Universiti Teknikal Malaysia Melaka, Malaysia
- Shajahan Maidin, Universiti Teknikal Malaysia Melaka, Malaysia
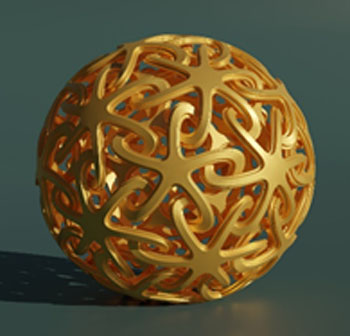
Scope
Additive Manufacturing has revolutionized the world of manufacturing. It offers innovative approaches to design, create, and repair a wide range of products, from simple prototypes to complex components. This disruptive technology has transformed traditional manufacturing paradigms, allowing for greater flexibility, customization, and cost-effectiveness. As the field of Additive Manufacturing continues to evolve, there is a growing need to explore new materials, methods, and applications to harness its full potential. To address these emerging trends and challenges, we invite researchers, engineers, and experts in the field to contribute to a special focus issue on "Additive Manufacturing Processes." This focus issue aims to showcase the latest advancements and insights in additive manufacturing, with an emphasis on exploring new frontiers, applications, and materials. Topics of interest include, but are not limited to:
- Materials and Material Development for Additive Manufacturing
- 3D Printing of Electronics and Functional Devices
- Additive Manufacturing in Healthcare: Bioprinting and Medical Devices
- Additive Manufacturing in Aerospace and Automotive Industries
- Design Guidelines and Software Tools for Additive Manufacturing
- Post-processing Techniques and Surface Finish
- Sustainability and Environmental Impact of 3D Printing
- Wire Arc Additive Manufacturing
Submission process
We encourage submissions from all authors whose work fits with the scope of this focus collection. The collection will also feature invited contributions. All focus issue articles are subject to the same review process as regular articles. Authors are invited to contact one of the guest editors, or the journal team directly, to discuss the suitability of their work prior to submission.
Please submit your article via our online submission form. You should submit the appropriate article type for your submission then choose 'Focus issue on Additive Manufacturing Processes' from the drop-down menu.
Deadline for submissions
The target deadline for submissions is 31 August 2024 though we can be flexible where necessary. We encourage early submission where possible, as articles will be published on acceptance without being delayed by other papers in the collection.
Participating Journals
Topical Review
Paper
This technical investigation used friction stir processing to modify the AA7075- T6 alloy and aimed to analyze the wear and impact toughness properties of the modified surfaces. Effects of the input parameters of the friction stir process (FSP) were also studied. Initially, the as-received AA-7075 alloy was processed using FSP at the selected parameters to get defect-free processed specimens. Next, the microstructures of the base alloy and processed regions were examined through an optical microscope. Then, the impact toughness was measured using the Charpy test, and sliding wear behavior was evaluated on a pin-on-disc tribo-tester. The processed samples' average impact energy was better than the base material's. Also, their wear property, i.e., coefficient of friction and weight loss, were more promising than the parent metal. Finally, fractography of the fractured Charpy test sampleswas done to study the fracture behavior; andSEM micrographs and 2D profiles of wear tracks were analysed to examine the wear behaviour properly.
Fused deposition modeling (FDM) is renowned as a prominent approach in the realm of 3D printing, where objects are built layer by layer using a heated nozzle to extrude melted materials. This research was conducted to identify the most effective FDM process variables to enhance tensile strength while simultaneously reducing surface roughness. Polylactic Acid (PLA) was chosen to fabricate test samples, showcasing the applications of 3D printing. In the course of this research, we conducted a series of 27 experiments to investigate the fundamental relationship between the parameters and the corresponding responses. The central aim of this study lies in optimizing the input variables viz. printing speed, layer thickness, and carbon deposition (C-deposition) for the technological manufacturing process of embossing parts in the context of Industry 4.0. To enhance both tensile strength and surface roughness simultaneously, a new hybrid method has been suggested. This approach integrates grey relational analysis (GRA) with principal component analysis (PCA) to determine the optimal combination of process parameters in the 3D printing process. Notably, the experiment trial exhibited the highest grey relational grade (GRG), indicating optimal process parameter settings at a printing speed of 100 mm s−1, layer thickness of 0.1 mm, and C-deposition of 15 mg respectively. Additionally, mathematical models are created through response surface methodology to explore the impact of FDM parameters on the grey relational grade. The findings from this study can be utilized in various industries and applications where FDM 3D printing is employed.
In the study high-velocity oxy-fuel thermal spraying to create Fe32Cr21Co21Al16Ti5B5 and Fe43Cr16Co12Al14Ti5B10, Fe32Cr21Co21Ni16Si5B5 and Fe43Cr16Co12Ni14Si5B10 coatings on Q235 steel substrates. Jet-type testing is used to examine the coatings' resistance to slurry wear. Researchers examined the surface to learn more about the erosion process. Taguchi analysis and a wear model confirm the significance of the selected important factors. The wear model's proposed mechanism shows remarkable agreement with the data. Coating loss may be attributed to several causes, including mixed ploughing, and cutting, platelet development, abrasion grooves, and cracking. The outcomes showed that the effect speed was the main contributing variable, the contribution ratio reached 65% to 70%, for the impact velocity of coating no 1 to 4. In contrast, it is recognized that impact velocity > impingement angle > erodent feed rate > erodent size is the most important sequence. Micro-cutting, mixed cutting, and ploughing were the essential disintegration systems for all coatings at low impingement points. In contrast, platelets were detected under normal impingement angles, as confirmed by SEM analysis. Both coatings seem to form passivation films, as shown by their greater Ecorr values relative to the substrate. Fe, Co, Cr, Al, and O all show up as peaks in XPS analyses.
The effectiveness of the magnetic abrasive finishing (MAF) process relies on several factors, including the brush's flexibility that varies across tools. This study aimed to optimize the results of five key parameters (voltage, finishing time, gap distance, rotating speed, and particle size) on surface roughness (SR) and microhardness (HV) using the grey relational analysis (GRA) method. Experimental work employed the Taguchi design with L27 trials in Minitab 17, involving five variables with three levels for each. The impact of these parameters on microhardness and surface roughness for stainless steel SUS420 bubble cups was assessed using Taguchi and regression analyses. The best roughness improvement and the most substantial enhancement in microhardness were individually obtained with the GRA method. This method assigned the best results for both surface roughness and microhardness. According to Taguchi analysis, the voltage parameter has the main or maximum parameter effect on grade, followed by gap distance, time, spindle speed, and particle size. It was found that the optimal parameters were the same as the input parameters.
This study presents a comprehensive framework for extended manufacturing with integrated 3D printing technologies, exemplifying a paradigm shift in the manufacturing landscape. The Digital Thread Integration establishes a dynamic foundation, enabling real-time collaboration and data flow throughout the product lifecycle. Leveraging advanced AI-driven optimization, Digital Design Platforms streamline designs, processing 1,000 iterations per hour, and recommending materials based on component requirements. On-Demand Manufacturing Hubs strategically placed globally achieve substantial reductions in lead times (48 h) and material waste (15%). The Cybersecurity Infrastructure ensures the sanctity of the digital environment, employing secure communication protocols and an Intrusion Detection System (IDS) responding to threats in milliseconds. The Data Analytics Hub contributes to continual improvement by analysing 100 GB of 3D printing data daily, generating 50 actionable insights weekly. User Interface and Accessibility initiatives empower the workforce through intuitive training modules and responsive help desks. In conclusion, this framework exemplifies secure, efficient, and data-driven extended manufacturing, positioning the industry at the forefront of technological advancement.
Additive manufacturing offers many benefits, yet it is confronted with the challenge of rough surfaces resulting from the appearance of seam lines on the printed parts due to the layer-by-layer printing process. This study investigates the effect of ultrasonic-assisted vapor smoothing on the surface roughness of 3D-printed ABS samples. The ABS samples were printed with an open-source FDM printer. The vapour smoothing process was conducted by applying acetone and altering the ultrasonic frequencies and times to 0 kHz, 10 kHz, and 20 kHz for the frequencies and 10 min, 20 min, and 30 min for the times. The surface roughness measurements were performed using a Mitutoyo SJ-301 surface roughness tester. The findings demonstrated enhancements in the quality of the surface, reduction in the visibility of layer lines, and improved surface smoothness for all the samples. From the ANOVA analysis, the average value of Ra for 30 kHz frequency is 2.57 μm, which is better than 3.19 μm for 10 kHz frequency. The manipulation of ultrasonic frequencies and exposure durations decreased surface roughness parameters, suggesting enhancement of the time to attain smoother surfaces. This work demonstrates the effectiveness of ultrasonic-assisted vapour smoothing as a feasible post-processing technique for enhancing surface quality in 3D-printed ABS-printed parts.
Additive manufacturing (AM), represented as a manufacturing process, which is easily applicable to intricate designs, is widely considered in a variety of industries as a simple and cost-effective solution that complements or replaces traditional manufacturing processes. However, due to the demanding properties of ink materials employing ceramic materials, more stringent considerations are required in selecting an appropriate printing technique and implementing the rheological properties of the ceramic ink suitable for the selected printing technique. Here, material extrusion (ME) was selected as a 3D technique applicable to ceramic materials, and the rheological requirements of ceramic pastes that maximize their printability in ME were scrutinized in detail. It was found that the viscoelastic properties of the ceramic pastes played an important role in determining the flowability, cumulative height, and overhang angles that can be allowed in ME. A new supporter system for overhangs, powder-on-demand supporter (PODS), was introduced to ME and demonstrated to understand if PODS can further extend the limits in cumulative height and overhang angles allowed in ME.
In this research study, a recessed gate III-Nitride high electron mobility transistor (HEMT) grown on a lattice matched β-Ga2O3 substrate is designed. This research investigation aims to enhance DC and RF performance of AlGaN/GaN HEMT, and minimize the short-channel effects by incorporating an AlGaN back layer and field plate technique, which can enhances electron confinement in two-dimensional electron gas (2DEG). A precise comparison analysis is done on the proposed HEMT's input characteristics, output characteristics, leakage current characteristics, breakdown voltage properties, and RF behaviour in presence and absence of AlGaN back layer in regards to field plate configuration. The inclusion of back barrier aids in raising the level of conduction band, which reduces leakage loss beneath the buffer, and aids in keeping the 2DEG to be confined to narrow channel. Furthermore, the field plate design offers an essential electric field drift between gate and drain, resulting to enhanced breakdown voltage characteristics.
This paper discusses the impact of integrating a vacuum system into a material extrusion 3D printing process for acrylonitrile butadiene styrene (ABS) and polylactic acid (PLA) materials. The study aimed to investigate the effect of a vacuum system on the dimensional accuracy of the printed samples. Upon completion of the printing process, the samples' dimensions were carefully assessed using a Coordinate Measuring Machine (CMM). The geometrical dimensions measured are the diameter, corner radius, fillet, thickness, width, length and angle. Based on the result obtained, the material has yet to reach 100% of the desired geometry, which was identified due to the shrinkage of the material after the printing process. The results show that the vacuum system improved material flow and reduced dimensional deviations by reducing air molecules and minimizing convection. The results indicated a significant enhancement in dimensional accuracy for both ABS and PLA samples when using the vacuum system. ABS samples showed a 4% increase in accuracy, while PLA samples exhibited a 2% improvement compared to samples printed without vacuum assistance. These improvements were achieved by optimizing process parameters such as layer height (0.15 mm), infill percentage (10%), printing speed (45 mm s−1), and bed temperature (60 °C). These parameters were selected to ensure finer details, improved precision, structural support, stability, better adhesion, and reduced warping.
The hybrid composite material, resulting from the fusion of human hair and Kevlar 29 synthetic fiber in a 10:1 ratio, reinforced with epoxy resin using the hand layup technique, underwent meticulous mechanical and thermal testing. The investigation encompassed tensile, flexural, and impact property evaluations, elucidating a notable enhancement in mechanical strength with a diminishing synthetic fiber content. Concomitantly, the composite exhibited commendable heat resistance in heat deflection tests, making it potentially suitable for applications in elevated temperature environments. Water absorption properties were scrutinized, revealing a correlation between reduced synthetic fiber content and diminished water absorption, implying heightened durability in diverse conditions. Microstructure analysis through SEM provided intricate insights into the internal composition. In summation, the composite, featuring a higher proportion of natural fibers and a lower proportion of synthetics, demonstrated superior mechanical attributes, optimal heat resistance, and reduced water absorption, showcasing its applicability in automotive and engineering domains, particularly in the fabrication of vehicle panels and components. The aim of this research represents a significant advancement in composite materials, offering a cost-effective solution that balances mechanical strength and thermal resistance. It suggests the potential for high-performance materials by combining natural and synthetic fibers, promising versatility across various applications.