Abstract
The article describes methods and techniques intended for designing and manufacturing scaled airplane models applicable in experimental flight testing. Reduced model with resized geometric dimensions should be constructed in such way to preserve similarity of its structural properties with properties of the real aircraft. Having kept the similarity of weight, stiffness and aerodynamic load distribution and maintaining properly scaled values of thrust-to-weight and wing loading ratios we can prepare scaled model showing in-flight features identical to the real airplane.
A series of measuring and technological activities have to be undertaken to develop full CAD model mapping airframe geometry and structure of the real aircraft. The process chain includes measuring, design and technological activities. The development of the geometry model includes: scanning outer geometry of the real airframe, development of the surface geometry model in the CAD environment and then introducing inner geometry items which together with outer skin face make a completely assembled model of the aircraft. For the needs of constructing scaled model the full-size CAD model has to be reduced. The structure of that resized model do not have to be the same as the real one. Materials and structural elements can be quite different but after assembling them the similarity of static and dynamic structural effects should be proved. Within the manufacturing phase there are some necessary stages like preparing molds for laminating components, milling solid elements, assembly of structural components, surface finishing of the model-body surface. The final model was subjected to a load test in a special test stand to check its deformability under specific load. In the same way the numerical static analysis of the full-size FEM model was conducted. The distribution of static displacement results obtained in both cases were compared. The other way of checking structural properties of the scaled model is comparable analysis of resonant vibrations. However, in this case, vibration measurements were not carried out and model verification stopped on a comparative analysis of construction mass distribution.
The procedure and results were elaborated on the example of the Tu-154M aircraft, of which the reduced model was developed in the Faculty of Mechatronics, Armament and Aerospace of the Military University of Technology (FMA MUT Warsaw, PL). Constructing and testing dynamically scaled model is one of many tasks solved in the framework of complex research project, of which the general purpose was to give numerical and experimental results useful in explaining the circumstances of the Smolensk disaster.
Export citation and abstract BibTeX RIS
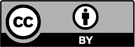
Content from this work may be used under the terms of the Creative Commons Attribution 3.0 licence. Any further distribution of this work must maintain attribution to the author(s) and the title of the work, journal citation and DOI.