Abstract
Nowadays, the JFRP composite is known as an eco-friendly, cost-effective, lightweight, higher stiffness product, and demand for this composite is increasing tremendously in various applications like automotive, aerospace, marine, and domestic upholstery. In order to achieve the required shape and design of this composite, machining is essential during the assembly stage. Thus, machining arises some difficulties in where surface roughness is one of the major drawbacks during machining of the milling process. The cutting parameter of machining influences the output performance of the product. The main purpose of this study is to find out the effect of milling parameters such as feed rate, spindle speed, depth of cut on the output responses like surface roughness, which generates during milling on JFRP composite. The machining was done by using a solid carbide cutting tool of 8 mm width and the experiments were conducted according to the Central Composite Design (CCD). It was found that whenever the spindle speed increases from 671.57 to 6328.43 rev/min then the Surface roughness decreases 18.58%. On the contrary, Surface roughness increased by 31.22% due to the increase in feed rate from 108.58 to 391.42 mm/min. A mathematical model was also developed in this study to correlate the milling parameters with the output parameter of the Surface roughness. It was found that the feed rate is the most significant factor to affects the Surface roughness. Based on the RSM, the predicted optimized input parameter were spindle speed 4293.8 rev/min, feed rate 1.50 mm/min, and depth of cut 1 mm in where Surface roughness would be lower (1.188 µm).
Export citation and abstract BibTeX RIS
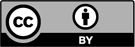
Content from this work may be used under the terms of the Creative Commons Attribution 3.0 licence. Any further distribution of this work must maintain attribution to the author(s) and the title of the work, journal citation and DOI.