Abstract
The adoption of hot rolled AHSS(Advanced High-Strength Steel) has been increased in accordance with the weight reduction of the chassis. The problem of tool life in punching the hole for high-strength steels is more important. Using the high-grade die material is one of the method to improve tool life. Another method for increasing the tool life is reducing the maximum punching load. We investigated the effect of tool shape on reducing the punching load. Conventional, shear-angled and humped tool geometry are considered for punching the flat sheets with 780MPa strength. In flat sheet, the maximum punching load is compared for each case of puch types. Maximum punching load is reduced by 40% of conventional punching process. For investigating the effect of punch shape in a real part, the punching process for the vent hole of the conventional wheel disc is modeled with FEM. The maximum load is efficeintly reduced by using the shear-angled punch.
Export citation and abstract BibTeX RIS
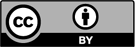
Content from this work may be used under the terms of the Creative Commons Attribution 3.0 licence. Any further distribution of this work must maintain attribution to the author(s) and the title of the work, journal citation and DOI.