Abstract
In this report, vulcan XC-72 supported PtNi alloy catalyst nanoparticles were synthesized by electroless deposition method using NaBH4 as a reduction agent. The properties of the synthesized Pt-Ni/C catalysts were investigated and evaluated. Transmission electron microscopy (TEM) results showed that PtNi alloy catalysts dispersed well on the carbon supports and their particle size was in the range of 4–8 nm. X-ray diffraction (XRD) analysis confirmed that the crystal lattice of Pt and PtNi alloy is face centered cubic. In the presence of Ni atom, an XRD pattern showed that structure of PtNi alloy crystal was contracted, which affected the catalyst's properties. The activity of the catalyst was estimated by electrochemical methods including cyclic voltammetry (CV) and linear sweep voltammetry (LSV). The electrochemical results indicated that the activity of PtNi/C alloy catalysts toward oxygen reduction reaction on cathode of PEMFC was higher in comparison with Pt/C catalysts.
Export citation and abstract BibTeX RIS

Original content from this work may be used under the terms of the Creative Commons Attribution 3.0 licence. Any further distribution of this work must maintain attribution to the author(s) and the title of the work, journal citation and DOI.
1. Introduction
Proton exchange membrane fuel cell (PEMFC) is a potential alternative power source in the future due to its advantages: fast start, high power density, low pollution. Carbon supported platinum nanoparticles are ideal catalyst material for the electrochemical reaction in PEMFC including hydrogen oxidation reaction (HOR) at anode and oxygen reduction reaction (ORR) at cathode [1–5]. However, platinum is a precious and expensive metal and this is one barrier to hinder mass application of PEMFCs. On the other hand, when Pt catalysts material is used as cathode, the rate of ORR on Pt is sluggish and the overpotential of ORR is higher, 250 mV, at open circuit potential 0.7 V, which reduces the conversion efficiency of PEMFCs [6–8].
Therefore, researches on new catalyst material with high performance and low Pt content in PEMFC have strongly been considered by scientists worldwide. Using Pt based alloy catalyst is an effective approche to reduce the overpotential of ORR and the content of Pt. The Pt-M binary alloy catalysts in which M is the transition metal (Ni, Co, Cr...) has high activity toward oxygen reduction reaction of the cathode which may take place following the direct four electrons mechanism without forming H2O2 intermediate product [8–13].
Among the Pt-M catalyst material, Pi-Ni/C alloy particles show the most potential for reducing the utilization of Pt in PEMFC. These catalysts have high activity for ORR and are preven` for CO poisoning. Moreover, some researches pointed out that the overpotential of PtNi/C alloy is lower than 80 mV and as a result the activity of alloy catalyst is 3–5 times higher in comparison with Pt pure. In preparation of alloy catalyst, the performance of catalysts alloy is considerably affected by the thermal treatment [12–19].
In this report, vulcan XC-72 supported PtNi alloy catalyst nanoparticles were synthesized by electroless deposition method. The properties of the synthesized PtNi/C catalysts were investigated and evaluated. The effects of content of Ni and heat treatment on the performance of the alloy catalysts in comparison with Pt/C were also discussed.
2. Experimental
2.1. Synthesis of Pt/C and PtNi/C catalysts material
Carbon vulcan XC72 supplied by Fuelcellearth (USA) is used as a support in the synthesis route. Before use, the supports were treated by heating at 500 °C for 2 h. After cooling by air, carbon material was washed with a huge amount of deionization water (DI) and was then dried at 100 °C for 1 h. The route of synthesis Pt/C and PtNi/C was as follows: carbon material was dispersed into a mixture of solvent including ethylene glycol and DI water. The precursors H2PtCl6.6H2O and NiCl2.6H2O (Merck, Germany) were then added with exactly calculated amounts in order to receive the catalyst having the metal content of approximately 20% wt. The mixture was ultrasonicated for 1 h and then an excess amount of NaBH4 reducing agent was added. Afterwards, the mixture was heated to 80 °C for 4 h. Finally, the given powder catalysts were washed by DI water and dried at 60 °C for 12 h. The carbon supported alloy catalysts samples with atomic composition in various ratios between Pt and Ni including Pt3Ni1, Pt2Ni1, Pt1Ni1, Pt1Ni2 and Pt1Ni3 were synthesized and a catalyst sample Pt/C was also prepared in the same conditions for comparison purposes. To investigate the influence of heat treatment, the alloy catalysts were heated in a tube oven under a reducing atmosphere 95% Ar + 5% H2.
2.2. Methodology
2.2.1. X-ray diffraction
X-ray diffraction method was used to investigate structure of catalyst materials. The samples were prepared by powder and analyzed by SIEMENS D5000 equipment with CuKα tube having power source 30 kW at Institute of Materials Sciences. The length wave of x-ray is 0.154 nm and 2θ scanning velocity is 0.04° s−1.
2.2.2. Transmission electron microscopy (TEM) method
The size and distribution of catalyst particles on the support were analyzed by transmission electron microscopy (TEM). The samples were captured by JEM 1010 apparatus (JEOL-Japan) with various magnifications at National Institute of Hygiene and Epidemiology.
2.2.3. Electrochemical methods
Electrochemical methods are popular to evaluate activity and durability of catalyst material employed in PEMFC. For electrochemical experiments, catalyst ink was prepared with the composition: 6 mg of catalyst, 6.2 mL of DI water, 2 mL of isopropyl alcohol, 16.2 μL of ionomer nafion solution 10%. The catalyst ink was stirred ultrasonically for 30 min before use. The catalyst layer was prepared by pipetting the catalyst ink on high density carbon samples. After each time for pipetting, the samples were dried under ambient condition. This process was repeated until reaching the calculated metal catalyst loading of about 0.4 mg cm−2.
The electrochemical experiments were conducted in a three-electrodes cell with platinum sheet as counter electrode and saturated calomel electrode as reference. The working area was controlled over 1 cm2 and the tests were carried out in H2SO4 0.5 M solution with potentiostat PARSTAT 2273 (EG&G–USA)
To evaluate catalyst activity, cyclic voltammetry (CV) were measured in the potential range 0–1.3 V (normal hydrogen electrode NHE) with scanning velocity 50 mV s−1. Before testing, the samples were polarized for 60 s at initial potential value. From the CV curve, it was easy to calculate the electrochemical surface area (ESA) expressing the activity of the catalyst. To examine the durability of the catalyst, the CV characteristic of the samples was measured in the potential range 0.5–1.2 V (NHE) with 1000 cycles and scan rate of 100 mV s−1. The changes in performance of the catalysts samples were evaluated by observing the decrease of the ESA values of the catalysts.
The improvement of alloy catalysts activity for ORR was estimated by linear sweep voltammetry (LSV) method. The potential range was scanned from 1 V to 0.7 V with scanning rate 1 mV s−1.
3. Results and discussion
3.1. Evaluation of performance of PtNi/C alloy catalyst particles
The cyclic voltammetry (CV) curves of catalyst samples: commercial Pt/C, synthesized Pt/C and Pt1Ni1/C in H2SO4 0.5 M solution are shown in figure 1. Generally, the CV curves of the three catalyst samples have the same shape. On the CV curves, there are electrochemical peaks corresponding to the different electrochemical reactions on the sample surface. In the potential range 0–0.4 V, the peaks express the adsorption/desorption processes of hydrogen on Pt crystal. In the forward scan, the potential range 0.4–0.8 V corresponds to the charge of the double layer by the oxygenated groups on the carbon support surface. At the potential of 0.85 V, the oxidation process of Pt metal happens to form Pt oxides. Corresponding with this process, there is a reduction peak at 0.7 V of reduction process of Pt–O in the reverse scan. Among the three CV curves, the voltammogram of synthesized Pt/C shows a high value. The alloy catalyst Pt1Ni1/C has a smaller peak area in comparison with both Pt/C catalysts. This may be related to the content of Pt and the size of catalyst particle in the alloy. On CV curve of the alloy catalyst, there is a slightly change of electrochemical peak and therefore, the electrochemical processes appearing on the alloy catalyst surface are affected by appearing Ni metal.
Figure 1. CV curves of commercial Pt/C, synthesized Pt/C and Pt1Ni1/C catalyst samples in H2SO4 0.5 M solution; scanning velocity 50 mV s−1.
Download figure:
Standard image High-resolution imageThe content of Ni also considerably affects the activity of the alloy catalysts Pt-Ni/C. Figure 2 presents CV curves of the carbon supported alloy catalysts samples Pt3Ni1, Pt2Ni1, Pt1Ni1, Pt1Ni2 and Pt1Ni3. When increasing the content of Ni metal, there is a slight decrease of the area of the electrochemical peaks which leads to the decrease of the ESA value of alloy catalyst. Table 1 shows ESA values of all catalyst samples calculated by integrating CV curves in H2SO4 0.5 M solution.
Figure 2. CV curves of the alloy catalysts samples with various content of (a) Pt and (b) Ni in H2SO4 0.5 M solution. Scanning velocity 50 mV s−1.
Download figure:
Standard image High-resolution imageTable 1. ESA values of alloy catalyst samples with various Ni content.
Sample | Pt3Ni1/C | Pt2Ni1/C | Pt1Ni1/C | Pt1Ni2/C | Pt1Ni3/C | Pt/C | Commercial Pt/C |
---|---|---|---|---|---|---|---|
ESA (m2 g−1 Pt) | 12.68 | 11.07 | 18.06 | 9.60 | 10.63 | 43.02 | 36.474 |
On the other hand, the content of Ni also affects the durability of the alloy catalysts Pt-Ni/C. Figure 3 shows the decrease of ESA values of alloy catalysts after 1000 cycles of durability tests. It might be clear to observe that the decline of ESA values is inversely proportional to the number of cycles. On the chart, the alloy catalyst Pt1Ni1/C shows moderate durability for PEMFC.
Figure 3. The change of ESA values of alloy catalyst samples after CV durability tests.
Download figure:
Standard image High-resolution image3.2. Effects of heat treatment on the performance of the alloy catalysts.
In the synthesis process of alloy catalysts, heat treatment plays an important role for improving the performance of alloy catalysts. After heating, undesired impurities are removed and the alloying process is also promoted, which leads to an increase of the distribution of catalyst particles on the carbon supports. To investigate the influence of heat treatment on the alloy catalyst performance, the samples Pt1Ni1/C were heated at various temperatures: 300, 500, 700 and 900 °C under a mixed atmosphere of 95% Ar and 5% H2. The change of structure of alloy catalysts was evaluated by x-ray diffraction method. An XRD pattern of the catalyst samples is displayed in figure 4. For Pt/C catalyst, the XRD result shows unsharpened and broad diffraction peaks and confirms that the structure of crystal lattice is face centered cubic. This may suggest that the size of the synthesized Pt particles is fine and structure of Pt may be amorphous. In the presence of Ni atoms, the XRD results are slightly changed. The 2θ values of peaks corresponding faces (111) and (200) are shifted toward higher value in comparison with the standard spectra of Pt metal. There are no peaks corresponding for Ni metal and its oxides on the XRD results. Therefore, the structure of alloy catalysts Pt1Ni1 is also fcc. They form a solid solution and the lattice of alloy material may be contracted. During co-deposition process, Ni atoms substitute randomly Pt atom positions in the lattice. Because the size of Ni atom is considerably smaller than the size of Pt atom, as a result lattice parameters of alloy material become smaller. With heat treatment the diffraction peaks of alloy material become sharper. The widths of the peaks are also narrowed considerably. This may be caused by transition of metal particles from amorphous to crystal and the size of these alloy particles becomes bigger due to alloying process.
Figure 4. XRD pattern of (a) Pt/C, of Pt1Ni1/C with heat treatment at various temperatures (b) 300 °C, (c) 500 °C, (d) 700 °C and (e) 900 °C.
Download figure:
Standard image High-resolution imageThe change of the size of catalyst particles is also observed in TEM pictures. Figure 5 presents the TEM pictures of vulcan support, the synthesized Pt/C and Pt1Ni1/C with heat treatment at various temperatures. On TEM pictures, the carbon supports are grey and in sphere shape with the size around 30–40 nm. There are black spots distributed uniformly which are the catalyst particles. For Pt/C catalysts the size of particles is about 2–3 nm while the alloy particles have bigger size, approximately 4–8 nm. After heating at 500 °C and 700 °C, the size of the alloy particles increases to 6–10 nm. The coarseness of alloy particles in heat treatment may be caused by alloying process. However, the distribution of alloy catalysts on the supports is improved significantly.
Figure 5. TEM pictures of Pt/C and Pt1Ni1 with and without heat treatment at different temperatures: (a) carbon vulcan-72, (b) the synthesized Pt/C, (c) Pt1Ni1/C without heat treatment, (d) Pt1Ni1/C with heat treatment at 500 °C, (e) Pt1Ni1/C with heat treatment at 700 °C.
Download figure:
Standard image High-resolution imageTo clearly understand the role of Ni metal in catalyst property for ORR, the LSV curves of the catalyst are measured in H2SO4 0.5 M solution. Figure 6 presents LSV curves of catalysts Pt/C, Pt1Ni1/C with and without heat treatment at 700 °C with scanning potential velocity 1 mV s−1. In the presence of Ni metal, oxygen reduction reaction on alloy catalysts might happen at more noble potential in comparison with Pt/C catalyst. Moreover, polarization current densities of alloy samples also increase. At the same potential value 0.75 V (NHE), the current density corresponding with alloy catalysts is considerably higher in comparison with the synthesized Pt/C catalyst. This may be explained as follows: due to the presence of Ni metal the absorption process of the oxygenated groups is decreased on Pt crystals. On the other hand, in a strong acid environment, mechanism of oxygen reduction reaction often takes place at different potential values with the following reactions:
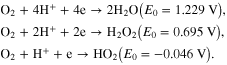
Figure 6. LSV curves in H2SO4 0.5 M solution of catalyst samples: Pt/C, Pt1Ni1/C and Pt1Ni1/C with heat treatment at 700 °C. Scanning velocity 1 mV s−1.
Download figure:
Standard image High-resolution imageTherefore, the decrease of intermediate groups leads to making oxygen reduction reaction become easier with the mechanism of four-electron direct exchange at potential value 1.229 V, which means that the efficiency of PEMFC reaches a high value. After heat treatment, the activity of the alloy catalyst still has higher activity for ORR in comparison with Pt/C. At small polarization current densities, the activity of the alloy catalyst reduces insignificantly compared to the alloy catalysts without heat treatment. This may concern the change of the size of alloy particles due to heat treatment. However, at high current densities, the activity of alloy catalysts becomes higher than that of alloy catalysts without heat treatment. These results indicate that with heat treatment the performance and stability of alloy particles are improved considerably.
4. Conclusion
The carbon vulcan XC72 supported alloy catalyst material Pt-Ni/C with different composition of Pt and Ni with smaller size than 10 nm were synthesized by the electrodeless deposition method. The size and structure of the alloy catalysts particles were affected by heat treatment; as a result the performance of these alloy catalysts was changed. The electrochemical results showed that the performance of Pt1Ni1/C alloy catalyst is considerably higher in comparison with Pt/C catalysts. The Pt1Ni1/C alloy catalyst with heat treatment at 700 °C gives high performance for oxygen reduction reaction in PEMFC.
Acknowledgments
This paper was completed with the financial assistance of Vietnamese Academy of Science and Technology (VAST) by the project VAST03.08/14–15 and the support of Institute of Materials Science (IMS).